
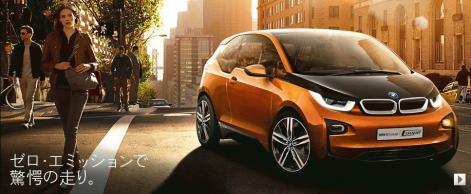
【BMW i】は、電気自動車およびプラグイン・ハイブリッドに特化したBMWの新しいサブブランドです。
その製品の第一弾である【BMW i3】のデビューが近付いてきました。
電気自動車であるi3には、様々な新しい技術が盛り込まれています。
その中でも最も意欲的な項目は、何と言っても車体骨格にCFRP:カーボン・ファイバー強化プラスチック(以下カーボンと略します)を用いることです。
カーボンはスチールやアルミとは段違いに軽量かつ強靭ですが、成形に非常に手間がかかり、製造コストが高くつくのが特徴です。
ちなみに今までに販売された車で、車体骨格にカーボンを用いた代表的な車を列記しますと・・・。
【メーカー名・社名】 発売開始年・発売当時のおよその価格
【ブガッティ・EB110】 1991年・ 4000万円
【マクラーレン・F1】 1993年・1億円
【フェラーリ・F50】 1995年・ 5000万円
【フェラーリ・エンツォ】 2002年・ 8000万円
【ポルシェ・カレラGT】 2004年・ 5000万円
【ベンツ・SLRマクラーレン】 2004年・ 5800万円
【ブガッティ・ヴェイロン】 2005年・1億6300万円
【アルファロメオ・8C】 2007年・ 2200万円
【アストンマーティン・One-77】 2010年・1億6000万円
【レクサス・LFA】 2010年・ 3750万円
【ランボルギーニ・アヴェンタドール】 2011年・ 4100万円
・・・と言ったところです。(^^;ゞ
「生産台数を少数に限った、超高価なスポーツカー」しか実例がありません。
「製造コストを度外視して、性能を最優先にできる車」ともいえると思います。
そのカーボン車体を、大量生産を前提としたコンパクトカーに採用することは、非常に画期的なことだと思います。
電気自動車は大容量のバッテリーを搭載することにより重くなりがちですが、
運動性能と航続距離の向上のために、BMWはカーボン車体を選択しました。
> 10年以 上にわたる研究と製造のノウハウを持つBMWは現在、SGLオートモーティブ・カーボン・ファイバーズ社とともに、炭素繊維や炭素繊維シートの開発・生産 を行っています。 という努力の成果です。
過去の数千万円以上のスポーツカーの多くが、「手作業と巨大なオーブンによって成形されるドライカーボン」を使用していたのに対し、近年は「熱可塑性樹脂や紫外線硬化樹脂を用いたRTM法」も開発されたことも、低コスト化へつながったものと思われます。
※CFRPやBMW iのカーボン車体に関しては、過去のブログ記事
【大胆な選択に隠れた野望?】や
【画期的な小型車戦略】でもご紹介しておりますので、ぜひご参照ください。
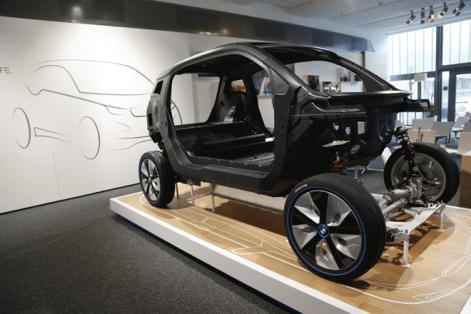
その画期的なi3の特性と製造技術に関して、
【「BMW i3」はそこまで来ている BMWイノベーション・デイに参加して】:webCG
で詳しく紹介されています。
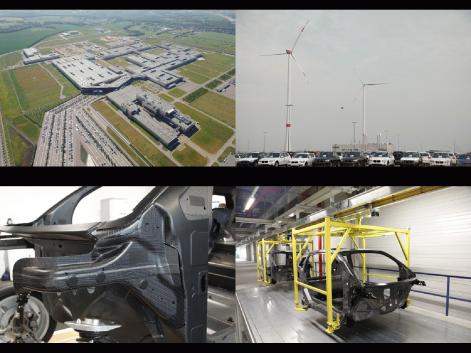
「生産拠点となるライプチヒ工場は、電力を全て風力発電で賄う」など、画期的な取り組みについても詳しく解説されています。
カーボン素材の採用が、生産・組立工程も含め省エネルギー・低公害につながっているとのことです。
(ちなみにライプチヒは旧東ドイツ地域でベルリンに次ぐ大都市だそうです。)
そして、私が以前から疑問に思っていたことへの回答も書かれていました。
カーボンは特性上、スチールやアルミの様に溶接や曲げ加工ができません。
事故を起こした後の破損部分の修理が難しいのでは? と懸念していたのですが..。
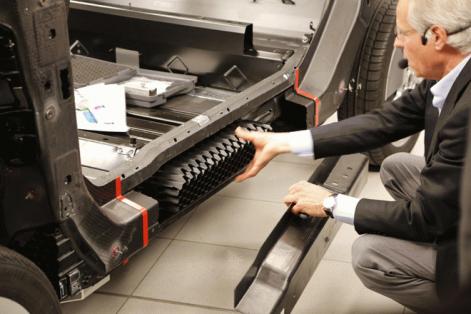
> CFRP製のライフモジュールは、リペアはそれほど難儀ではない。破損部分をカットして新しいパーツを組み付ける作業は、スチールモノコックボディーの鈑金(ばんきん)よりはるかに簡単だ。
とのことです!安心しました。
要するに、破損部分をカットして、補修用部品を接着するのだと思います。
それどころか、
> そもそもCFRPは外部には露出しておらず、外板パネルに覆われている。しかもそれは傷のつきにくいサーモプラスチック製だけに、普段使いでの小さな傷などはかえって少なくなりそう。総じてi3は、従来の車種より保守・維持費用が20%ほど安く抑えられるというから意外である。
とのことです。
これで私もカーボン車体の採用を全面的に喜べます(^^;ゞ
( 画像はi8のレーシングカー仕様のイメージです )
i3のデビューが待ち遠しいのはもちろんですが、
軽量で強靭なカーボン車体をもつ【i8】の登場もますます楽しみになってきました。
BMWが掲げる【EfficientDynamics】は、燃料の向上・排出ガス低減を実現しながら、同時に比類なきパフォーマンスを追求します。
BMWは、BMWにしか創りだせない未来を見せてくれそうです! G.Sekido